Le contrôle qualité est une procédure mise en place par les entreprises qui visent à s’assurer de la conformité d’un produit.
Il est exécuté par un contrôleur qualité avec l’aide (ou non) des autres acteurs de la production.
La conformité est établie à partir des critères développés par l’entreprise ou par un commun accord entre un fournisseur et un client. (On y inclus par exemple la métrologie industrielle.)
Cette démarche volontaire permet à l’entreprise de répondre à des problématiques de qualité des produits dans un marché toujours plus exigeant.
Assurer la qualité des produits est devenu indispensable pour les entreprises, non seulement pour répondre aux exigences des clients, mais aussi parfois pour des raisons légales.
Sommaire
Introduction au Contrôle Qualité
Définition
Le contrôle qualité représente une procédure (ou une série de procédures) visant à assurer la qualité d’un produit manufacturé.
Dans cette optique, le produit doit satisfaire un ensemble défini de critère de qualité et d’exigence client.
Attention, on associe souvent Assurance Qualité avec Contrôle Qualité, mais les définitions ne sont pas exactement les mêmes !
Contrairement à la procédure de contrôle, qui vise à identifier les potentielles non-conformités, l’assurance qualité vise, elle, à empêcher la fabrication de produits non-conformes.
En français, ça veut dire que l’assurance qualité intervient durant le processus de fabrication du produit, là où le contrôle qualité intervient une fois le produit fini. Les deux sont souvent regroupés sous une seule entité.
En général, cette procédure vise à répondre aux normes de qualité en vigueur, et apporter ainsi des labels ou certifications à l’entreprise ou au produit.
Conformité et non-conformité
Avant d’aller plus loin, faisons un petit point sur ce qu’est la conformité !
La conformité est actée lorsque le produit passe l’intégralité des tests de qualité avec succès.
Le produit est conforme et il peut passer à l’étape suivante. (assemblage, commercialisation, etc.)
Lorsque les produits ne sont pas conformes, il est nécessaire d’effectuer une action (ou plusieurs !) afin de passer l’audit.
Une non-conformité, c’est le non-respect d’une exigence. Cela passe principalement par la détection de la cause racine, puis on s’intéresse à la non-conformité : le produit est il retouchable ou est-il à jeter ?
Les missions de contrôle
L’objectif de l’inspection, c’est de détecter des non-conformités.
Au bon moment..
Et surtout, d’identifier les causes et conséquence qu’elle pourrait produire.
Détecter des problèmes est une bonne nouvelle pour l’entreprise.
Vous êtes ainsi en mesure d’identifier et de corriger les problèmes lorsqu’ils subviennent.
Les sources de non-conformité sont nombreuses et il serait justement inquiétant de ne jamais détecter de problèmes.
Distinguons deux types de contrôles pour la suite.
Le contrôle à réception
Vous devez vous assurer que les produits reçus d’un fournisseur passent les audits prévus.
Dans ce cas de figure, vous n’êtes pas maître de la fabrication du produit, vous vous devez donc de vérifier qu’il est bien conforme à vos exigences.
En général, on effectue l’audit avant la mise en stock.
Le contrôle en fin de production
Lorsque vous êtes le fabriquant du produit, vous devez également faire subir des examens à votre produit.
En effet, vous avez beau être maître de la production, un dysfonctionnement pourrait se glisser dans votre processus et vous vous devez de certifier la conformité de votre produit à vos clients.
Dans ce cas de figure, le contrôle qualité vous permet d’identifier les dysfonctionnements et de les régler rapidement et réactivement.
Comment réaliser un contrôle qualité
Il existe différentes manières de réaliser un contrôle. En premier lieu, distinguons les méthodes. Ils en existent deux :
- Le contrôle à 100%, ou systématique. Dans cette méthodologie, le contrôleur cherche à contrôler l’intégralité des pièces du lot.
- Le contrôle par échantillonnage. A l’inverse du contrôle à 100%, on ne contrôle qu’une partie du lot, un échantillon représentatif.
Les deux méthodes ont leurs limites, mais il est important d’en distinguer les grandes lignes. Si vous contrôlez chacune des pièces, vous serez limité en plusieurs points :
- Le coût sera beaucoup plus important, puisque vous effectuez plus de contrôles.
- Vous ne pourrez pas réaliser de contrôles destructifs et serez limités aux techniques de contrôles non-destructifs. (Dont Plastiform ! et si vous y jetiez un coup d’œil ? 😉)
- En contrôlant à plus grande fréquence, vous augmentez le risque d’erreur humaine.
À l’inverse, le contrôle par échantillonnage va vous limiter en termes de performance, vous ne contrôlez pas tout, donc vous êtes susceptible de louper une malfaçon.
C’est assez rare et c’est pour ça que cette méthodologie est largement utilisée.
Le plan de contrôle
Peut importe la solution dans laquelle vous vous trouvez, vous devrez avoir une méthodologie millimétrée.
Le plan de contrôle des processus (PCP) est un document formel qui permet de définir les étapes nécessaire à la validation de conformité d’un processus ou d’un produit.
Ce document est spécifique au produit ou processus.
Le plan permet de vous assurer que le produit correspond aux exigences en assurant la documentation de celles-ci. En général, le PCP est représenté en tableau et comporte les éléments suivants :
- L’identifications des points de contrôle,
- Les caractéristiques à contrôler (quel type ? indicateur, variable, etc. par exemple : dimensions en mm.),
- Les tolérances,
- La fréquence sur échantillonnage,
- La méthode de contrôle et l’instrument de mesure,
- Les actions à effectuer en cas de non conformité.
N’oubliez pas bien entendu de répertorier convenablement le plan en lui attribuant un identifiant unique.
Réagir face à une non-conformité
La détection d’un défaut de fabrication relève d’une situation de crise.
En effet, si vous constatez une anomalie, vous allez avoir à résoudre plusieurs problèmes.
D’abord, vous allez devoir identifier le problème (ce qui n’est pas toujours évident), ensuite vous allez devoir le réparer, puis relancer une batterie de tests.
Durant ce laps de temps, vous ne pouvez plus produire. Non seulement vous ne pourrez plus produire, mais vous allez devoir effectuer des correctifs sur ce qui a déjà été produit, voire pire, perdre les produits.
Ainsi, il est primordial d’être réactif et de pouvoir réagir rapidement durant toutes les étapes, à savoir :
- Réaliser des contrôles non-chronophages, pour détecter le plus tôt possible les malfaçons (Attention ! Rapide ne veut pas dire bâclé !)
- Être réactif sur la détection de l’origine. Si vous contrôlez votre produit en toute fin de chaîne, vous aurez par exemple bien plus de sources potentielles de problèmes que si vous effectuez un contrôle à chaque étape.
- Vous devrez aussi être réactif sur la remise en conformité de la chaîne de production, ce qui veut dire que vous avez une procédure claire et établie.
Les types de contrôle
Être réactif, c’est aussi sélectionner les bons outils.
Lorsqu’il est question d’effectuer un contrôle de la qualité d’un produit, vous avez trois options qui s’offrent à vous :
- Détruire la pièce pour effectuer le contrôle en effectuant un contrôle destructif. C’est une option coûteuse et parfois très chronophage, mais elle vous sauve si vous n’avez pas de solution.
- Contrôler sans détruire via des solutions de contrôle non-destructif. En fonction de la solution, c’est plus ou moins long, mais c’est en général plus économique que de détruire la pièce. (En particulier si vous utilisez Plastiform)
- Le contrôle indirect délocalisé. C’est un champ spécifique du contrôle non-destructif. Le contrôle ne s’effectue plus sur la pièce, mais sur son empreinte, et l’empreinte sert de témoin de la mesure. (et facilite ainsi la traçabilité du contrôle)
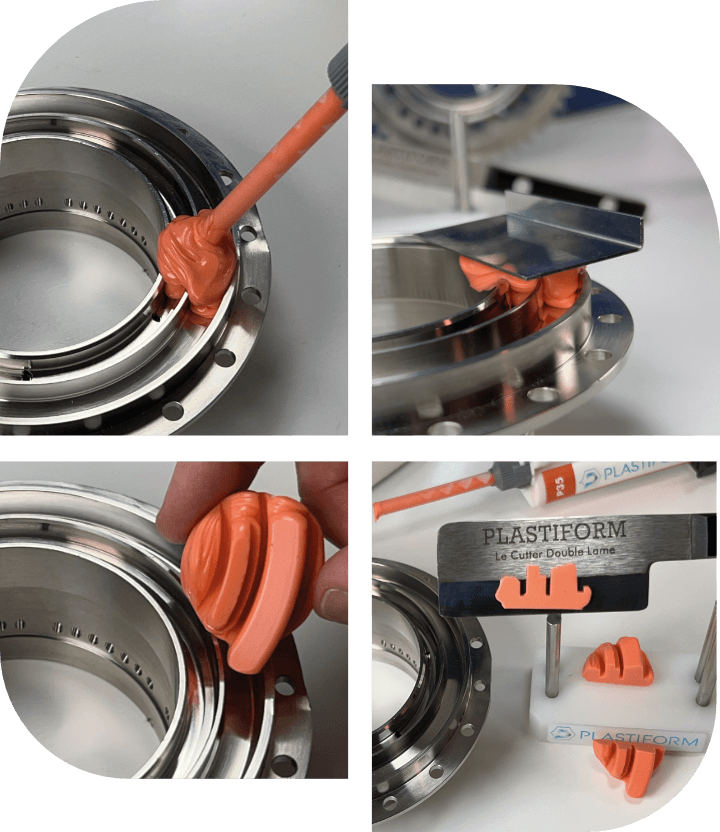
Il est important de déterminer à l’avance vos procédés de contrôle avec une réflexion poussée pour optimiser au maximum ce processus.
Il est également important de mettre en place une veille permanente pour améliorer continuellement vos méthodes.
Conclusion
De nos jours, il est primordial de mettre en place une démarche de contrôle qualité dans les entreprises. Que ce soit par souci interne de proposer des produits qualitatifs, ou par obligation législative ou contractuelle, le contrôle qualité est une réalité dont vous devrez faire face.
On distingue deux types de contrôle qualité, le contrôle à réception, et le contrôle en production. Dans les deux cas, l’objectif est de détecter des anomalies sur les produits.
Il existe différentes méthodologies afin d’effectuer le contrôle qualité. Vous pouvez premièrement effectuer un contrôle à 100%, en testant chacune des pièces d’un lot, ou vous pouvez opter pour un contrôle par échantillonnage, en ne sélectionnant qu’une partie des pièces du lot.
Dans les deux cas, il est important d’être efficace dans la détection et le traitement des non-conformités afin de ne pas pénaliser la rentabilité de l’entreprise.
Ne pas détecter rapidement l’origine d’un problème, voire pire, le problème en lui-même, pourrait provoquer un arrêt de la chaîne ou la production de pièces non-rattrapables, ce qui est un problème !
Plastiform est une solution innovante de contrôle non destructif qui permet de réaliser des contrôles rapides et très efficaces de dimension, ou de l’état de surface. C’est une solution qui prend à peine quelques minutes et dont l’empreinte reste témoin, vous pouvez ainsi la réclamer à votre fournisseur pour valider le contrôle à réception.