Le Contrôle Non Destructif (CND), appelé également Essais Non Destructif ou Évaluation Non Destructive, est une discipline regroupant des procédés et techniques qui permettent de mesurer et d’assurer la conformité et l’intégrité d’un matériau ou d’une pièce sans avoir à la détruire ou à l’altérer. Le contrôle non destructif peut même aller jusqu’à éviter un démontage ou un déplacement de pièce.
L’utilisation des techniques de mesures sans destruction est primordiale pour l’industrie. En effet, les techniques de CND sont très importantes pour une entreprise car elles permettent de faire beaucoup d’économie en ne détruisant pas des pièces qui peuvent parfois être très coûteuses.
Il existe aujourd’hui plusieurs techniques très populaires de d’évaluation non destructive. L’industrie de la métrologie et du contrôle qualité perfectionnent ces technologies d’année en année et leur permettent de remplacer de plus en plus le contrôle destructif, encore trop présent dans l’industrie.
Sommaire
Applications Principales du Contrôle Non Destructif
Le CDN est appliqué dans la quasi-totalité des secteurs industriels. En particulier : l’aéronautique, l’aérospatiale, l’industrie pétrolière, le ferroviaire, le nucléaire, les énergies, l’automobile etc.
Lorsque les opérateurs emploient les évaluations non destructives, ils cherchent à mettre en évidence des défauts susceptibles d’altérer la conformité du produit. L’opérateur recherche principalement des défauts qui concernent les dimensions, l’usure, la géométrie ou encore la présence de malfaçons.
Les Évaluations non destructives permettent ainsi au fabricant d’assurer la conformité des produits qu’il vend mais également à l’acheteur d’assurer la conformité des produits qu’il réceptionne. Également, le CND permet de contrôler l’usure d’un produit tout au long de sa durée de vie. Cela permet, entre autres, d’assurer la sécurité d’un produit, tout au long de son utilisation, par exemple d’un avion en circulation.
Lorsque l’on pratique un examen non destructif, nous sommes à la recherche principalement de 3 types de défauts :
- Une non-conformité au cahier des charge : Mesures dimensionnelles incorrectes, état de surface incorrecte, Angles incorrectes, etc.
- Les défauts de surface : des trous, des fissures, des piqûres, etc.
- Des défauts interne : des marques d’usure, de la porosité, des fissurations, des variations d’épaisseur, etc.
Par cette procédure, il est possible de garantir l’objectivité et la reproductibilité d’un contrôle effectué sur une production. Ces procédures sont basées sur des normes (en général ISO) avec des codes et des spécifications propres à certaines industries, Et s’inscrivent dans un processus de maîtrise des risques pour l’entreprise.
Les Techniques de Contrôle Non Destructif (CND)
Il existe énormément de techniques mais cinq d’entre elles sont particulièrement utilisées par l’industrie de nos jours. Ces cinq techniques permettent d’effectuer la majorité des contrôles, mais certaines d’entre elles peuvent s’avérer parfois très coûteuse en matériel.
La Magnétoscopie
L’examen magnétoscopique est un contrôle par champ magnétique dont la valeur est définie en fonction de la pièce. C’est une des techniques de contrôle non destructif les plus anciennes (avec le ressuage) qui permet, entre autres, de détecter des discontinuités de surface. Cette technique ne peut cependant s’appliquer que sur des matériaux ferromagnétiques (matériaux sensibles aux aimants).
La magnétoscopie ne permet de détecter que des discontinuités débouchantes ou légèrement sous-jacentes, par exemple, des criques, fissures ou tapures.
Il est relativement simple de réaliser un essai non destructif magnétoscopique. Il vous suffit de magnétiser la zone à contrôler afin de créer une fuite du champ magnétique vers les discontinuités. La fuite entraîne les particules ferromagnétiques vers la discontinuité, et c’est ce phénomène qui vous permettra de voir le défaut.
Il existe plusieurs types de matériel pour réaliser ses contrôles en général ce sont des aimants portatifs ou du matériel permettant de mettre la pièce sous tension.
Enfin, pour faciliter la vision du défaut, les surfaces sont souvent recouvertes par des particules ferromagnétiques fluorescentes nommées révélateurs.
Le Ressuage
Cette technique d’essai non destructif ne permet de mettre en évidence que les discontinuités débouchantes. Le ressuage est compatible avec une très grande variété de matériaux à l’exception des matériaux trop poreux.
Pour réaliser un examen de ressuage, vous devez faire pénétrer un produit dans les discontinuités, tout en lui permettant de sortir.
Pour cela, la pièce doit être enduite d’un liquide appelé “pénétrant” coloré ou fluorescent (ou les deux !). Le liquide va alors pénétrer par capillarisation à l’intérieur des défauts de la pièce à contrôler. Après un temps de repos, la surface doit être nettoyée et séchée avant d’être recouverte à nouveau d’une couche mince d’un produit dit “révélateur”, un produit avec la capacité d’absorber le liquide pénétrant.
Si un défaut est présent sur la pièce, le révélateur va mettre en évidence le pénétrant qui s’était infiltré dans le défaut l’opérateur pour alors, à l’oeil nu, constater la présence de discontinuités débouchantes sur la surface.
La Radiographie
Comme pour la radiographie en médecine, la radiographie industrielle consiste à faire traverser une pièce par un faisceau de rayon X afin d’irradier un film placé à l’arrière de la surface à contrôler. La radiographie peu être utilisée sur tous les types de matériaux.
Les défauts sont mis en évidence par une variation de densité optique sur le film. Plus un défaut est important plus il sera visible sur le radiogramme. Par exemple pour une surface scène de 22 mm d’épaisseur une porosité de 2.7 mm sera bien plus visible qu’une porosité de 1.4 mm.
Plusieurs dispositifs sont capables d’effectuer une radiographie dans l’industrie, un accélérateur linéaire, les équipements de gammagraphie, ou des équipements à rayons X par exemple.
Le Contrôle par Ultrason
Cette méthode de contrôle vise a propagé à l’intérieur de la pièce des ondes ultrasonores qui agiront différemment en fonction des discontinuités et des surfaces qu’elles rencontreront. Le contrôle par ultrason est utilisable sur la quasi-totalité des matériaux mais le comportement des ondes est influencé par la structure de ces derniers (la taille du grain par exemple).
le choix de la fréquence des ondes permet d’améliorer la sensibilité de détection du contrôle une onde est-elle vais par exemple 5 MHz plus elle sera sensible. À l’inverse, si la surface à contrôler et grossière il faudra plutôt privilégier des ondes basse fréquence par exemple 2MHz.
Le Contrôle par Prise d’Empreinte
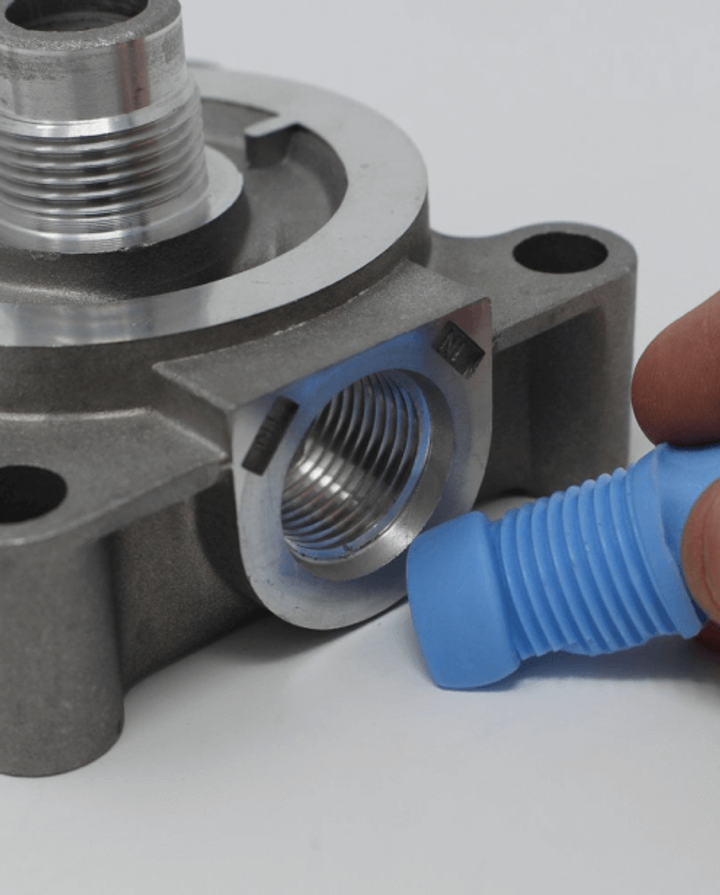
La prise d’empreinte et notre spécialité chez Plastiform ! Cette procédure de contrôle vise à injecter un produit à l’origine liquide ou pâteux sur la surface ou dans la pièce dont vous souhaitez vérifier la conformité. Les produits étant des bi-composants, leur mise en contact dans la pièce ou sur la surface provoque une réaction de polymérisation qui va faire durcir le liquide.
Une fois le liquide dur, vous disposerez d’une empreinte négative parfaite de votre pièce ou de votre surface. Vous n’avez plus qu’à l’extraire grâce aux propriétés élastiques du produit.
La prise d’empreinte, et en particulier les Plastiforms, ont pour avantages d’être utilisable sur la quasi-totalité des matériaux. Surtout, ils permettent de mettre en évidence énormément de défauts : les dimensions, les angles et la géométrie de la pièce, l’état de la surface, la rugosité de surface, la présence de micro défaut, etc.
Parmi les cinq techniques de contrôle non destructif présentées ci-dessus, le contrôle par prise d’empreinte est l’une des moins coûteuse avec pour en moyenne 5$ par contrôle.
Le Contrôle Non Destructif Par Plastiformisation
Les contrôles non destructif par prise d’empreintes sont assez récentes comparées aux autres techniques et procédures utilisées dans le secteur. Pour aller un petit peu plus loin sur le sujet, je vais détailler dans cet article quelques aux intérêts que vous pourriez trouver à utiliser cette technique.
Les principaux avantages de la technique
Le premier point important, c’est la précision des empreintes. Bien que le mot empreinte puisse avoir une connotation assez négative dans les esprits, les empreintes Plastiform ont une très grande précision. Les empreintes sont identiques à la cavité à plus ou moins 1 μm. Cette précision est d’autant plus importante que vous utilisez du matériel de qualité pour les analyser. Par exemple avec des machines de mesure sans contact (projecteurs de profil, interféromètres, etc.) vous obtiendrez de meilleure précision avec une machine de mesure avec contact.
Second point, également très intéressant, la traçabilité que peuvent fournir les empreintes. Les empreintes Plastiforms, une fois extraites, ne changent pas, c’est-à-dire que leurs dimensions où les défauts qu’elles ont capturé resteront, y compris plusieurs années plus tard. Grâce à cette spécificité il est possible pour les entreprises d’assurer une traçabilité de leur contrôle en conservant les empreintes ainsi que les relevés de mesures effectuées grâce à elle.
ESSAYER PLASTIFORM DÈS MAINTENANT
La mallette contient tous les accessoires nécessaires pour utiliser Plastiform. C’est la meilleure façon d’essayer nos solutions pour la première fois !
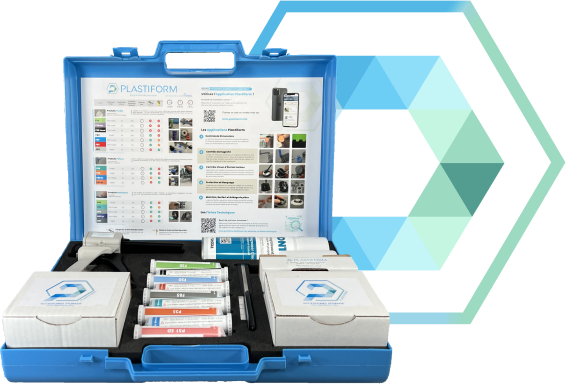
Également comme signalé un petit peu en amont, la prise d’empreinte est un procédé assez économique dont le coût est estimé à environ 5$ par contrôle. Ce faible coût permet aux entreprises d’effectuer des contrôles systématiques sur leur production ne sacrifiant ainsi ni du temps, ni de l’argent.
Enfin, un énorme avantage que peuvent avoir les produits de prise empreinte, et en particulier ceux que nous commercialisons chez Plastiform, c’est qu’il est possible de les appliquer sans déplacer ou démonter la pièce. Si vous constatez des défauts sur une production nécessitant de contrôler des produits en circulation (par exemple des avions), vous n’aurez pas besoin de les démonter pour effectuer le contrôle avec l’empreinte. Cette particularité, bien que peut-être un peu situationnel, fait parfois gagner énormément d’argent et de temps aux entreprises qui pourraient se retrouver en difficulté dans un cas de figure pareil.
En d’autres termes les contrôles non destructif par prise d’empreintes (ou par Plastiformisation) sont une méthode très pratique pour vérifier la conformité d’une pièce mais aussi pour mesurer son usure dans le temps.
Conclusion
Pour conclure sur cet article, chaque méthode de contrôle non destructive propose des paramètres différents à prendre en compte. Il est important de noter le type de discontinuité que vous recherchez, le matériau sur lequel vous recherchez cette discontinuité et quelles sont les contraintes l’entreprise.
Il n’existe pas une technique meilleure que toutes les autres. Chaque technique dispose de ses propres points forts qui la rendent parfois évidente pour effectuer un contrôle non destructif. C’est au contrôleur de décider de quelle technique il a besoin et de sa mise en œuvre. Il est ainsi important de faire le bilan afin de déterminer s’il n’y a pas une meilleure manière de procéder pour gagner en précision en temps et en argent.