无损检测涵盖了一系列工艺与技术,其核心目的在于识别材料的特征差异、焊接缺陷及不连续性,而这一切都在不损伤原始部件的前提下完成。
无损检测技术在工业领域中扮演着至关重要的角色。对于企业而言,技术的价值尤为凸显,因为它能够在不损坏昂贵部件的情况下,帮助企业显著节约成本。
当今,已有多种无损检测技术广受青睐。计量与质控行业不断推动这些技术的革新与完善,旨在逐步取代在工业生产中仍较为普遍的破坏性测试。
目录
无损检测的主要应用
无损检测的应用遍及几乎所有工业领域,例如:航空航天、石油、铁路、核能、能源、汽车等行业。
操作员使用无损检测的目的,是找出那些可能影响产品合格性的瑕疵。他们主要关注尺寸、磨损、几何形状等方面的偏差,以及是否存在其他缺陷。
因此,无损评估不仅能帮助制造商确保其产品的合格性,也能让采购方对收到的产品质量放心。此外,NDT技术还可以在产品的整个生命周期内监控其磨损状况,这对于保障产品使用期间的安全性至关重要,例如确保飞行中飞机的安全。
在进行无损检测时,主要关注以下三类缺陷:
- 与规格不符:尺寸偏差、表面粗糙度超差、角度不符等。
- 表面缺陷:孔洞、裂纹、点蚀等。
- 内部缺陷:磨损痕迹、气孔、内部裂纹、厚度变化等。
遵循既定程序,可以确保对生产批次进行检验的客观性与可重复性。这些程序通常基于ISO等国际标准,并结合特定行业的规范与准则,是企业风险控制体系的重要组成部分。
无损检测 (NDT) 技术
无损检测技术种类繁多,其中五种在当今工业界的应用尤为广泛。这五种技术能满足绝大多数的检测需求,但部分技术所需的设备投入可能相当高昂。
磁粉检测
磁粉检测利用磁场进行测试,磁场强度会根据待检部件进行设定。它与渗透检测同属最古老的无损检测技术之列,主要用于探测表面不连续性。然而,该技术仅适用于铁磁性材料(即易于被磁化的材料)。
磁粉检测仅能探测到开口于表面或位于近表面的不连续性,例如裂纹和裂缝。
磁粉检测的操作流程相对简单:首先对被检区域进行磁化,在不连续处会形成磁泄漏场。该泄漏场会吸附施加在表面的铁磁性颗粒,从而将缺陷直观地显示出来。
执行此类检测的设备有多种,常见的是便携式磁轭或能对部件施加电流的设备。
最后,为了让缺陷更容易被发现,检测表面通常会覆盖一层被称为显像剂的荧光铁磁性颗粒。
渗透检测
该无损检测技术仅能揭示开口于表面的不连续性。渗透检测适用于多种材料,但表面过于疏松多孔的材料除外。
渗透检测的原理是让某种液体(渗透液)渗入缺陷中,之后再通过特定方法将其“引出”以显示缺陷。
具体操作时,需先在部件表面涂覆一层被称为“渗透剂”的液体,该液体可为着色或荧光类型。渗透剂会通过毛细作用渗入待检部件的表面缺陷中。经过一段时间的渗透后,需将表面多余的渗透剂清洁干净并干燥,再均匀喷涂一层薄薄的“显像剂”,这是一种能够吸附渗透液的特殊材料。
如果部件表面存在缺陷,渗入其中的渗透剂就会被显像剂吸附出来,从而在表面形成清晰的痕迹,让操作员用肉眼就能观察到这些开口缺陷。
射线照相法
工业射线照相法的原理与医用X光类似,即让X射线或伽马射线穿透工件,并使放置在其后方的胶片感光。该技术几乎适用于所有类型的材料。
胶片上图像的黑度变化可以凸显缺陷的存在。通常,缺陷尺寸越大,在射线底片上形成的影像就越清晰。例如,在一个22毫米厚的工件上,一个2.7毫米的气孔影像会比1.4毫米的气孔影像明显得多。
工业射线照相所使用的设备多种多样,例如线性加速器、伽马射线探伤仪或X光机。
超声波检测
该检测方法的基本原理是在工件内部发射超声波,声波在遇到不连续性(如缺陷)或界面时会发生反射或衰减。超声波检测几乎适用于所有材料,但声波的传播特性会受到材料微观结构(如晶粒尺寸)的影响。
通过选择合适的超声波频率可以优化检测的灵敏度。通常,频率越高,检测灵敏度也越高,能发现更小的缺陷。但另一方面,如果被检表面较为粗糙,则最好使用穿透力更强的低频波(例如2MHz)。
无损印模检测
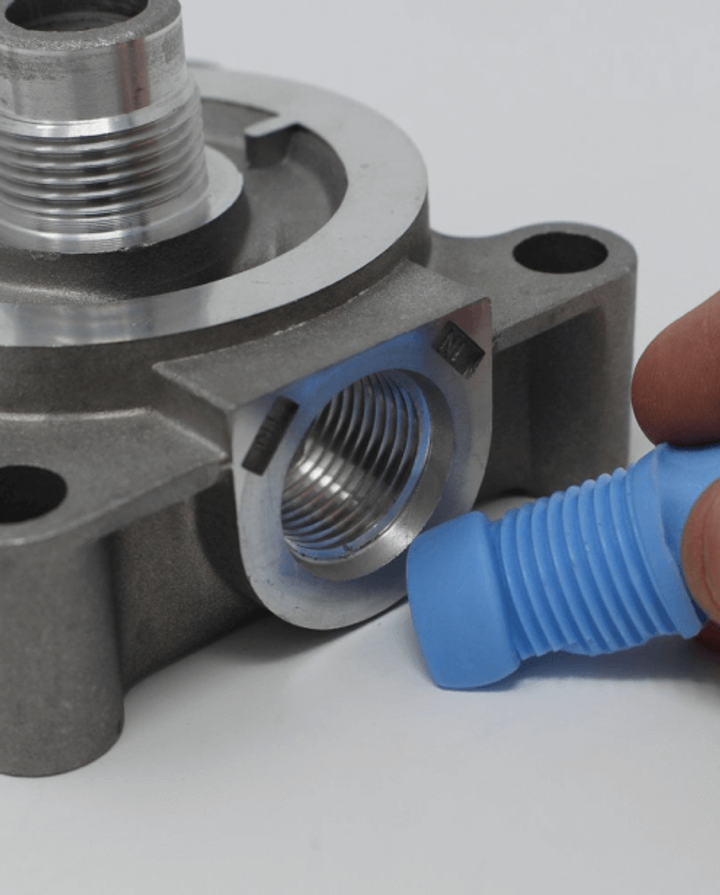
在Plastiform(复制胶泥),印模检测正是我们的专长!该检测方法是将一种液态或膏状的材料注入待检部件的内部或涂覆于其表面。我们的产品是双组份材料,混合后会发生聚合反应,迅速固化。
材料固化后,便会形成一幅完美的部件或表面阴模(或称“反向复制品”)。之后,只需利用材料本身的弹性,即可轻松将其从工件上取下。
印模检测,特别是Plastiform(复制胶泥)产品,其优点在于几乎适用于所有材料。更重要的是,它能够精确复制并用于检测多种特征,例如:部件的尺寸、角度和几何形状,表面状况,表面粗糙度,以及是否存在微小缺陷等。
在前述五种无损检测技术中,印模检测是成本最低廉的方法之一,平均每次检测的成本仅为5美元左右。
使用Plastiform(复制胶泥)进行无损检测
与工业界其他传统技术相比,印模无损检测是一项相对较新的方法。下面,我们将深入探讨该技术能为您带来的独特优势。
该技术的主要优点
首先是精度。尽管“印模”一词听起来可能很简单,但Plastiform(复制胶泥)印模的精度极高:复制品与原始型腔的误差在±1 μm以内。当使用高精度的测量设备(如轮廓投影仪、干涉仪等非接触式测量设备)对印模进行分析时,这种高复制精度尤为关键,它能确保测量结果的准确性,甚至优于直接对工件进行接触式测量。
其次是可追溯性。Plastiform(复制胶泥)复制品一经固化成型,其物理形态便十分稳定,所复制的尺寸和缺陷信息即使在数年后也不会改变。正是由于这一特性,企业可以通过保存印模及相关的测量记录,轻松实现检测结果的长期追溯。
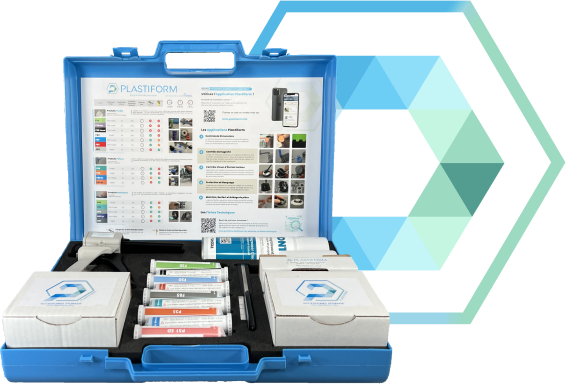
此外,如前文所述,印模检测是一种十分经济的方案,单次检测成本预估仅为5美元。低廉的成本使企业能够对其产品进行更系统、更频繁的检测,而不会造成巨大的财务或时间压力。
最后,Plastiform(复制胶泥)印模产品还有一个巨大优势:无需移动或拆卸部件即可现场应用。当您需要检测正在使用中的产品(如飞机发动机叶片)时,无需进行复杂的拆解,即可完成检测。这一特性虽然在某些特定场景下才能完全体现其价值,但对于面临此类挑战的企业而言,无疑能节省大量的时间和金钱。
总而言之,印模无损检测是一种非常实用的方法,既可用于检查部件的初始合格性,也可用于追踪其在使用过程中的磨损情况。
结论
总而言之,每种无损检测方法都有其独特的适用范围和考量因素。在选择具体方法时,必须综合考虑待检缺陷的类型、工件的材质以及企业自身的限制条件(如成本、效率要求等)。
不存在所谓“最好”的技术,只有“最合适”的技术。每种方法都有其独特优势,在特定应用场景下会成为不二之选。检测人员需要根据具体情况,决定采用哪种技术以及如何实施。因此,全面评估检测需求,从而找到兼顾效率与成本的最佳方案,才是明智之举。