Non-Destructive Testing (NDT) is a discipline grouping together processes and techniques to identify characteristic differences, welding defects, and discontinuities, all while avoiding any harm to the original part.
The use of non-destructive testing measurement techniques is essential for the industry. Indeed, NDT techniques are very important for a company because they allow to make a lot of savings by not destroying parts that can sometimes be very expensive.
Today there are several very popular Non-Destructive Testing techniques available. The metrology and quality control industry is perfecting these technologies year after year, allowing them to increasingly replace destructive testing, which is still too present in the industry.
Table of Contents
Main Applications of Non-Destructive Testing
Non Destructive Testing is applied in almost all industrial sectors. In particular: aeronautics, aerospace, oil industry, railways, nuclear, energy, automotive, etc…
When operators use non-destructive testing, they are trying to highlight defects likely to alter the conformity of the product. The operator is mainly looking for defects concerning dimensions, wear, geometry, or the presence of defects.
Non-destructive evaluations thus enable the manufacturer to ensure the conformity of the products it sells but also enable the buyer to ensure the conformity of the products it receives. Also, NDT allows controlling the wear and tear of a product throughout its lifetime. This makes it possible, among other things, to ensure the safety of a product throughout its use, for example, of an aircraft in circulation.
When performing a non-destructive examination, we are mainly looking for 3 types of defects :
- A non-conformity with the specifications: Incorrect dimensional measurements, incorrect surface finish, incorrect angles, etc.
- Surface defects: holes, cracks, pitting, etc.
- Internal defects: wear marks, porosity, cracks, thickness variations, etc.
With this procedure, it is possible to guarantee the objectivity and reproducibility of an inspection carried out on a production run. These procedures are based on standards (generally ISO) with codes and specifications specific to certain industries and are part of a risk control process for the company.
Non Destructive Testing (NDT) Techniques
There are many non-destructive testing techniques, but five of them are particularly used by industry today. These five techniques allow the majority of tests to be carried out, but some of them can sometimes be very costly in terms of equipment.
Magnetic Testing
Magnetic particle inspection is a magnetic field test whose value is defined according to the part. It is one of the oldest non-destructive testing techniques (with dye penetrant testing) which allows, among other things, to detect surface discontinuities. However, this technique can only be applied to ferromagnetic materials (magnet sensitive materials).
Magnetic particle inspection can only detect open or slightly underlying discontinuities, e.g. cracks, fissures, or tapers.
It is relatively simple to carry out non-destructive magnetic particle testing. All you have to do is magnetize the area to be inspected in order to create leakage of the magnetic field to the discontinuities. The leakage carries the ferromagnetic particles towards the discontinuity, and it is this phenomenon that will allow you to see the defect.
There are several types of equipment to carry out these checks, in general, they are portable magnets or equipment to energize the part.
Finally, to make it easier to see the defect, the surfaces are often covered by fluorescent ferromagnetic particles called revealer.
Penetrant testing
This non-destructive testing technique can only reveal open discontinuities. Penetrant Testing is compatible with a very wide variety of materials except for materials that are too porous.
To perform a PT test, you have to make a product penetrate into the discontinuities while allowing it to come out.
For that, the part must be coated with a liquid called “penetrant”, colored or fluorescent (or both!). The liquid will then penetrate by capillarization inside the defects of the part to be inspected. After a rest period, the surface must be cleaned and dried before being covered again with a thin layer of a product called “developer”, a product with the capacity to absorb the penetrating liquid.
If a defect is present on the part, the developer will highlight the penetrant that had infiltrated the defect the operator to then, with the naked eye, observe the presence of open discontinuities on the surface.
Radiography
As for radiography in medicine, industrial radiography consists in passing an X-ray beam through a room in order to irradiate a film placed behind the surface to be controlled. Radiography is most commonly used on all types of materials.
The defects are highlighted by a variation in optical density on the film. The more important a defect is, the more it will be visible on the radiogram. For example for a 22 mm thick stage surface a porosity of 2.7 mm will be much more visible than a porosity of 1.4 mm.
Many devices are capable of performing radiography in industry, such as linear accelerators, gamma radiography equipment, or X-ray equipment.
Ultrasonic Control
This control method aims to propagate ultrasonic waves inside the room that will act differently depending on the discontinuities and surfaces it encounters. Ultrasonic inspection can be used on almost all materials but the behavior of the waves is influenced by the structure of the material (grain size for example).
The choice of the frequency of the waves makes it possible to improve the sensitivity of the detection of the control. For example, the more sensitive a wave is, the more sensitive it will be. On the other hand, if the surface to be controlled is coarse and coarse, it is better to use low-frequency waves, for example, 2MHz.
Non-Destructive Impression Taking control
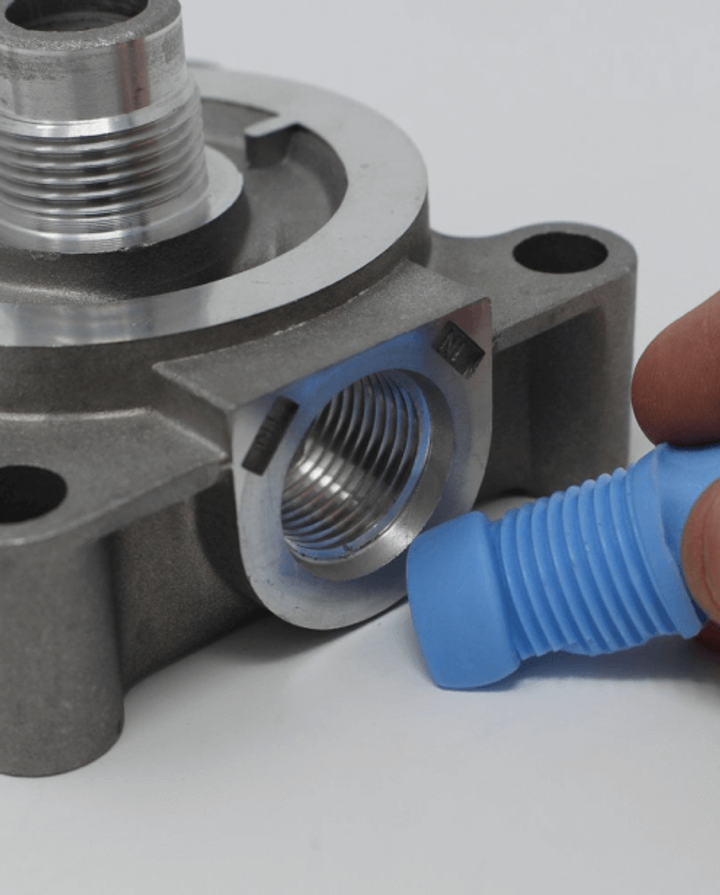
Impressions are our specialty at Plastiform! This control procedure aims at injecting a product, originally liquid or pasty, on the surface or in the part whose conformity you wish to check. As the products are bi-components, their contact in the part or on the surface causes a polymerization reaction which will harden the liquid.
Once the liquid has hardened, you will have a perfect negative imprint of your part or surface. All you have to do now is to extract it thanks to the elastic properties of the product.
The advantages of impression taking, and Plastiforms in particular, are that it can be used on almost all materials. Above all, they make it possible to highlight a large number of defects: the dimensions, angles, and geometry of the part, the state of the surface, surface roughness, the presence of micro defects, etc.
Among the five non-destructive testing techniques presented above, inspection by impression taking is one of the least expensive with an average of $5 per inspection.
Non-Destructive Testing With Plastiform
Non-destructive testing by impression taking is fairly recent compared to other techniques and procedures used in the industry. To go a little further on the subject, I will detail in this article some of the interests you might find in using this technique.
The main advantages of the technique
The first important point is the accuracy of the impressions. Although the word print can have a rather negative connotation in people’s minds, Plastiform prints have very high accuracy. Replicas are identical to the cavity to within plus or minus 1 μm. This precision is all the more important as you use quality material to analyze them. For example with non-contact measuring machines (profile projectors, interferometers, etc.) you will achieve better accuracy with a contact measuring machine.
The second point, also very interesting, is the traceability that prints can provide. Plastiforms replicas, once extracted, do not change, i.e. their dimensions where the defects they have captured will remain, even several years later. Thanks to this specificity it is possible for companies to ensure traceability of their control by keeping the prints as well as the records of measurements made thanks to it.
TRY PLASTIFORM NOW
The case contains all required accessories to use Plastiform. It is the best way to try our solutions for the first time!
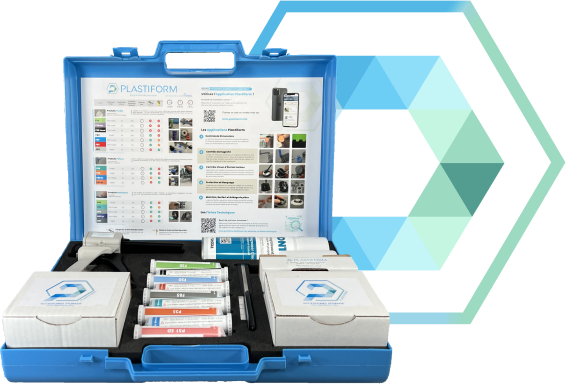
Also, as mentioned a little earlier, impression taking is a fairly economical process whose cost is estimated at about $5 per control. This low cost allows companies to carry out systematic controls on their production without sacrificing either time or money.
Finally, an enormous advantage of impression products, especially those we sell at Plastiform, is that they can be applied without moving or dismantling the part. If you find defects in a production process that requires testing products in circulation (e.g. airplanes), you will not need to disassemble them to perform the test with the replica. This feature, although perhaps a bit situational, sometimes saves a lot of money and time for companies that could find themselves in trouble in such a situation.
In other words, non-destructive testing using impressions is a very practical method for checking the conformity of a part but also for measuring its wear over time.
Conclusion
To conclude this article, each non-destructive testing method has different parameters to be taken into account. It is important to note the type of discontinuity you are looking for, the material on which you are looking for this discontinuity, and what the company’s constraints are.
There is no technique that is better than any other. Each technique has its own strengths that sometimes make it obvious for non-destructive testing. It is up to the inspector to decide which technique he needs and how to implement it. It is therefore important to take stock of the situation in order to determine if there is not a better way to proceed to save time and money.