提到表面处理中的遮蔽工序,我们首先想到的或许就是成卷的遮蔽胶带。其目的是保护零件的特定区域免受处理过程的影响。然而,这项操作通常漫长而乏味,不仅耗费大量人力,也离不开粘合剂的使用。
遮蔽胶带是工业领域最常见的遮蔽工具,但它远非理想之选。
实际上,胶带不仅需要手动粘贴,而且是一次性消耗品,无法重复使用。尽管如此,许多人似乎并未意识到还有其他选择。那么,我们究竟该如何替代它呢?
目录
什么是遮蔽?
如果您会点开这篇文章,想必对“遮蔽”并不陌生。不过,为了确保我们对接下来的内容有共同的理解,我们还是快速回顾一下它的核心目标。
当我们需要对一个零件进行处理时(例如喷漆、喷砂或化学处理),往往需要保护某些特定区域不受影响。这一步骤确保了只有预定区域会接触到处理工艺。
实现这种局部保护,最直接的方法就是使用遮蔽胶带,将其粘贴在需要保护的表面上。
胶带的优势在于其粘性,能够紧贴于零件表面。这一点,再加上其低廉的价格,使其得到了广泛应用。在大多数情况下,它确实可靠又实用,足以胜任任务。
为什么要更换遮蔽胶带?
但是,如果遮蔽胶带能满足基本需求,我们为什么还要寻找替代品呢?
的确,胶带能够保护需要遮蔽的区域,从而满足了基本要求(尽管效果并非总是完美,这一点我们稍后会详细探讨)。
正因如此,全球大多数公司在进行表面处理时,都会采用胶带进行防护。
然而,用作遮蔽的胶带存在诸多弊端,促使许多用户开始寻找替代方案。
其中主要问题包括:
- 操作繁琐: 胶带必须手动逐片粘贴。这是一个高度重复的过程,不仅耗费时间,也增加了人力成本。
- 一次性使用: 零件处理完毕后,遮蔽胶带必须撕除。它无法在不同零件间重复使用,每次都需重新粘贴。
- 综合成本高: 尽管胶带本身单价不高,但考虑到前两点,它实际上是一种成本高昂的遮蔽技术。
- 效果与精度: 胶带粘贴的精度难以保证,因遮蔽不当而导致零件损坏的情况时有发生。
不难看出,这些问题对企业而言可能造成严重损失,尤其是在处理过程中损坏零件的情况。
所有这些因素都促使企业积极寻找成本更低、实施更便捷的遮蔽胶带替代方案。
解决方案:复制胶泥 (Plastiform)
针对合作伙伴普遍遇到的这一难题,我们决定将复制胶泥 (Plastiform) 产品投入遮蔽应用测试。
与胶带不同,复制胶泥可以根据零件的形状定制成型。这一特性在创建可同时容纳多个零件的定制化模具方面,展现出无与伦比的优势。
如此一来,您只需一次操作即可为多个零件做好遮蔽,从而大幅提升生产力。
虽然制作模具的初始操作可能比贴胶带耗时略长,但由于模具可重复使用,从长远来看,您将节省下可观的操作时间!
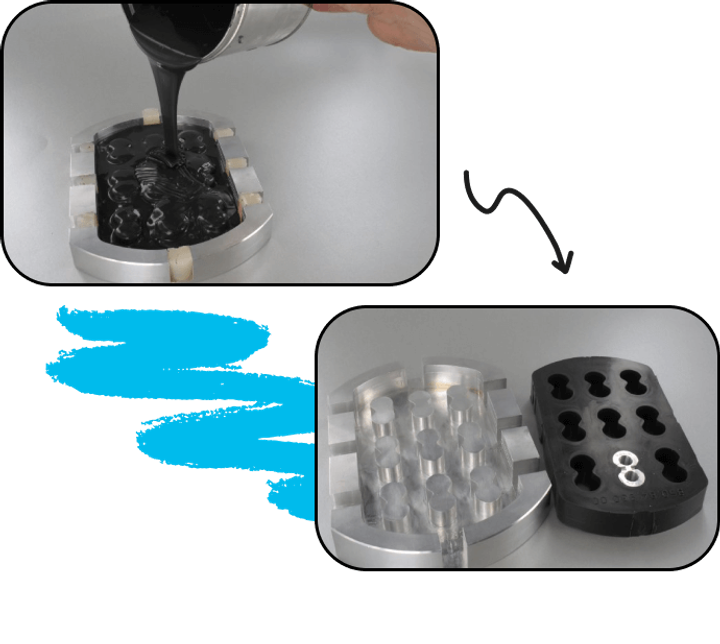
而这还不是复制胶泥在零件保护应用中的唯一优势。
大多数表面处理工艺都不会损坏复制胶泥模具,使其成为一种极其可靠、可重复使用的保护工具。
总而言之,复制胶泥能为您带来以下核心优势:
- 可重复使用:模具可多次重复使用,并能同时保护多个零件。
- 高精度和密封性:其精度可达微米级,产品能如吸盘般紧密贴合表面,确保绝佳的遮蔽效果。
- 高弹性:模具可具备高弹性,即使是形状复杂的零件也能轻松脱模。
综上所述,由复制胶泥制成的模具是替代遮蔽胶带的绝佳方案。它不仅克服了胶带的诸多弊端,其微米级的精度更确保了远超传统胶带的保护效果。
如何用复制胶泥替代胶带?
我们已经知道,复制胶泥是遮蔽胶带的一种理想替代品,但具体该如何操作呢?
从概念上讲,这非常简单——您只需在零件上制作一个保护模具或进行局部保护即可。
不同类型的模具
使用复制胶泥,您可以制作出不同类型的保护模具。每种模具都适用于特定的应用场景,因此,关键在于确定哪种方案最能满足您的需求。
话虽如此,有些模具比其他模具更常用。
在工业应用中,我们经常遇到相似的遮蔽难题,许多公司都面临着同样的挑战。
以下是一些常用模具的示例。它们涵盖了我们遇到的90%以上的零件遮蔽问题:
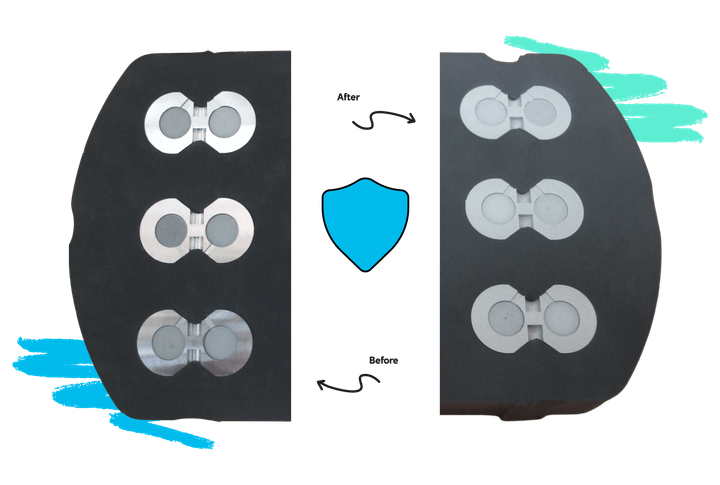
这是一种块状模具,可以同时容纳大量小零件。
其原理是将零件无需处理的部分嵌入模具中,仅暴露待处理的表面。
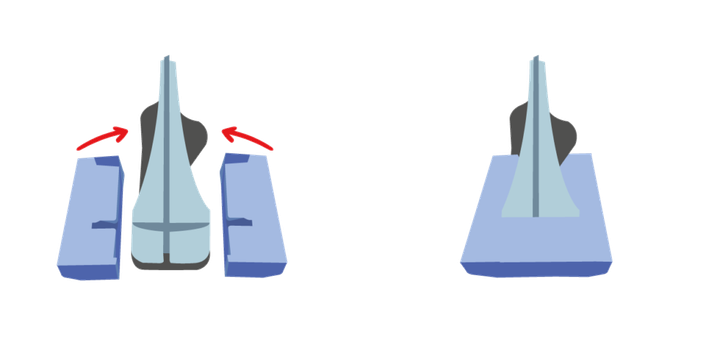
这种模具的设计则更为精巧!
它通常用于形状复杂的零件,当您只想保护其中特定一部分时,它便能派上用场。
该模具由两部分组成,使用时需将其围绕零件合拢并固定。

这并非传统意义上的模具,而更像是堵头或局部保护体。
这类保护通常是针对特定情况制作的,不一定都能重复使用。但其优势在于,相比胶带,它们的施用更方便,最重要的是,精度要高得多。
如何制作保护模具
制作模具或许是整个流程中最需要巧思的一步。
但与耗费数小时的繁琐胶带粘贴工作相比,这几分钟的巧妙构思又算得了什么呢?
我们在此不赘述局部保护体的制作,因为其施用方法与制作传统的复制胶泥印模类似。
让我们来区分两种主要情况:多零件保护模具和复杂形状保护模具。
对于第一种情况,即多零件保护模具,其制作过程通常相当简单,只需三步即可完成:
- 第一步:选择产品。 根据需求选择合适的产品。通常,需要弹性时可选 F30 XL;需要更高刚性时则可选 F50 XL 和 F70 XL。
- 第二步:制作基底。 找一个尺寸合适的容器,注入 2 到 5 厘米厚的产品,等待其固化(约 35 分钟)。
- 第三步:定位零件。 将零件放置在已固化的复制胶泥基底上,确保待处理的表面朝上。然后,继续浇注产品,直至完全覆盖所有需要保护的区域。
大功告成!
只需等待产品聚合(至少 35 分钟),您的定制模具就制作完成了。有了它,您可以轻松取出处理好的零件,再放入下一批,循环往复。
接下来我们看看第二种情况,这类模具的制作相对复杂一些。
这类模具的针对性非常强,需要围绕零件的特定待保护区域进行包裹。
因此,其制作需要形成一个两部分(或多部分)的“蛤壳式”模具,并在模具两侧预留出夹紧区域,以便将其固定在零件上。
要制作这种模具,您有两种选择:
- 第一种选择:联系我们的专家,由我们为您定制模具。
- 第二种选择:参照第一类模具的制作方法,自行制作,但关键在于要设计成两部分或多部分结构。
如果您选择自行制作,最复杂的步骤是在设计阶段规划好夹紧机制。在动手之前,请务必仔细构思您的模具方案。
结论
恭喜您!通过这次探索之旅,我们共同寻找到了传统遮蔽技术的创新替代方案。
正如我们所见,依赖胶带的传统遮蔽方法存在诸多缺陷:成本高、耗时长、精度低,且操作繁琐。
相比之下,定制化的复制胶泥模具在表面处理的保护任务中,则展现出卓越的效果和可靠性。
对我们的解决方案还有疑问? 欢迎随时联系我们!